My Career with Staples
From November 2023 to the present I have worked at the Staples in Warwick RI. Here I see hundreds of customers I work with every day to help them very quickly get what they need from holiday cards, to blueprints, fliers, booklets and anything else they can need. From my end, when a customer comes to me, I need to figure out exactly what they need, and offer the best options possible to get them what they need as quickly and at the best price possible. My top goal is customer satisfaction with speedy service and helpfulness.
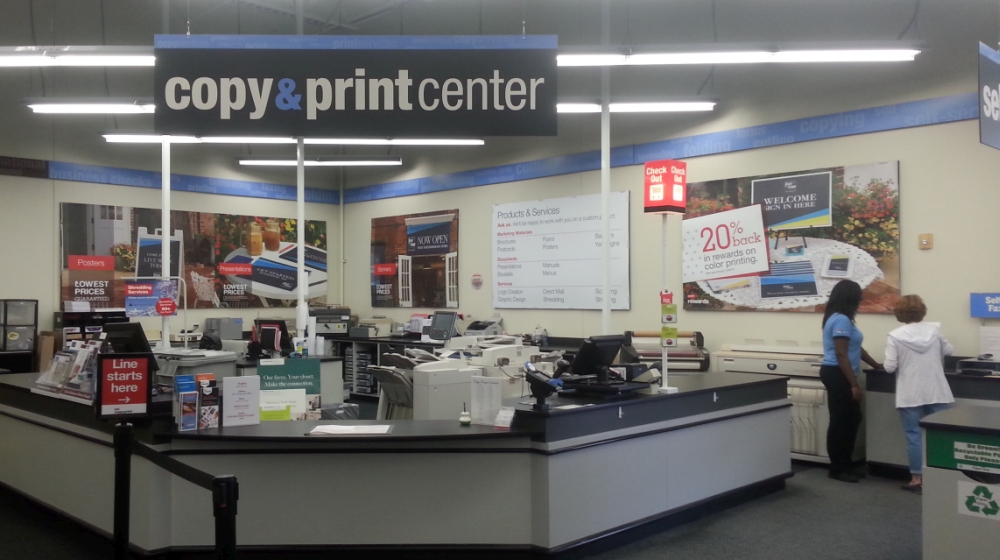
Daily Summary
A day in the life of a print and marketing associate generally follows a little something like this. After clocking in dropping my coat and lunch off I come to my station.
Generally my top priority is always any customers at the counter. I want everyone to out of the store as quickly as I can get them out with everything they came in for and give them the best price and customer service possible while they are in the store. I help them navigate what they want, and how I can make copies for them, and how long it will take. Sometimes they need help mailing items and I help with their needs in shipping and returning items.
When the customers are all set I do quality checks of other print associates work, everything gets checked before it is marked ready for pick up.
When quality checks are all set, I get to the fun part, making orders. It varies a lot on the time of year, but generally we have about 10-20 orders to do at once and usually they come in as fast as we finish them. Leaving as little work as possible for anyone coming in tomorrow or later on in the day is the goal. Leaving a totally completed order list is always something I want to do however. A list of different orders I work on can be found here
When my day is all set, I refill all of the machines with stacks of paper, usually about 2,000 – 5,000 sheets of paper. The copiers are checked for if they need ink, the laminators are shut off and the business card cutter is emptied. The returns bins are taped up and sent to ship out if they’re full and new boxes are made. Finally if I have the time or it’s the proper day for it, I vacuum and clean the counters.
Printing Knowledge
As a Staples print and marketing associate I needed to do several different tasks for customers when they come into the store.
- Simple printing (Generally through the Staples website, but also through their phones, computers, thumb drives or physical copies they have with them. The most common is through the website or right on their phones which means I need to have the best skills for communication with customers who have difficulty sending emails. It sounds simple but many customers are of different age ranges and some do not speak English so working with them is key to getting their prints.)
- Poster printing
- Lamination and mounting
- Bound booklets and folded prints (these require certain folding machines and binding hole punchers to be completed, which are two machines that require additional operation knowledge.)
- Business cards (some cards are printed and then cut by a machine made for business cards cutting, however some papers are too thin and the machine is too rough with them so they need to be hand cut.)
- Post cards / Holiday cards (needs hand cutting and stacks range from 25-250 per order)
- Scanning (used for editing, making pdf copies of items and duplicating blueprints)
- On the spot editing (sometimes people need edits made and photoshopping photos to make them fit frames)
- Shipping services (USPS, UPS, Express Return, and Happy Return. A big part of the job is also quickly identifying Amazon returns since that is another department and I need people to go over to them without being upset since they went the wrong way.)
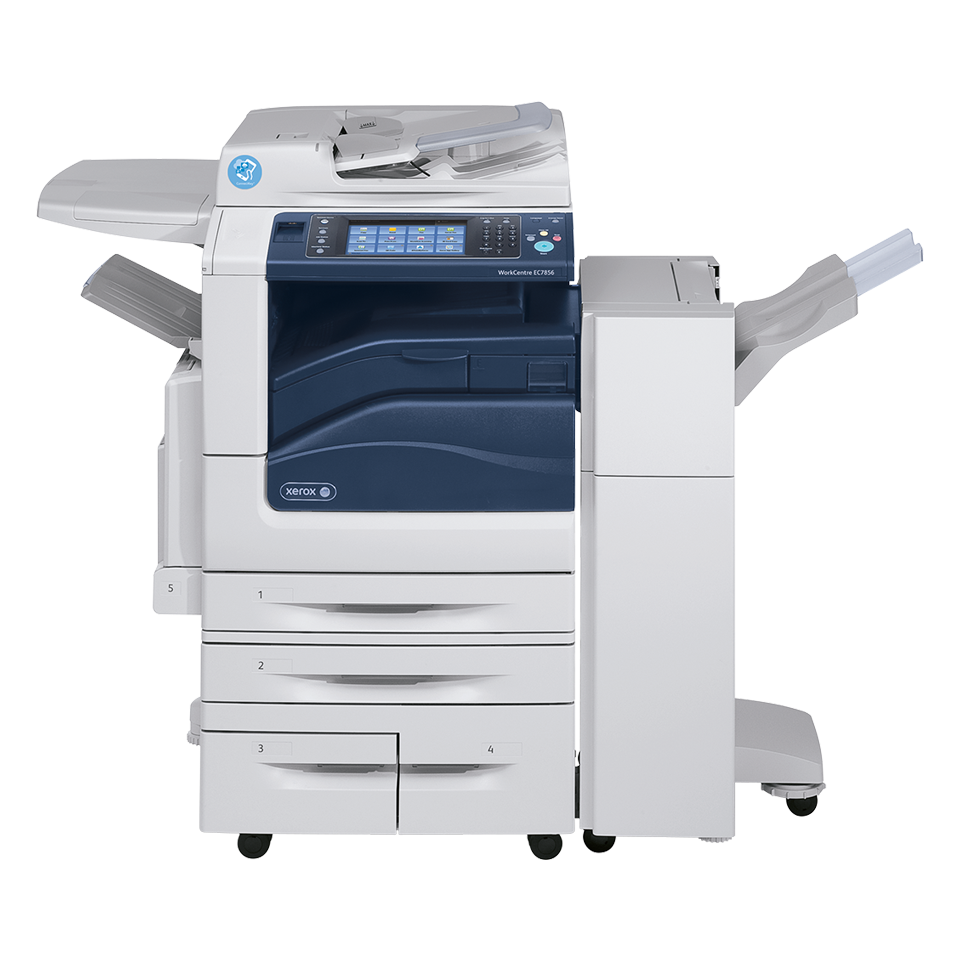
What I Bring to the Job
While other people also work in my department I stand out among them as different in my own ways. I find I generally am quicker to respond to customers than others and I always have a positive attitude. My managers are always surprised at how high my tolerance is and I find helping people is always worth trying my hardest. It’s easy to get bitter for some people but really making things for other people and having them enjoy it is why I love making things in the first place.
I am a trained graphic designer and know how to use the full adobe and Microsoft suite of software. Customers can come to me with requests and edits needed that other associates just can’t do since they lack my level of experience and understanding of these tools.
Photo editing example right here.
Or here on my social media.
Interesting Orders
- A customer has no file with them, however they want to have a banner made for an event.
Generally this means there is nothing that can be done, they need to go to our website and use a premade template and design the banner themselves and we can make it with the file sent from our website. However, this customer was an older person, so I sat with them and designed the banner myself. They were very fickle with the design and struggled to articulate basic concepts like what color they wanted it, trying to describe bright green as “more yellow than yellow”. I was able to help them make the banner and they were very grateful for my all my efforts in the design and how quickly I made it. - A customer needs 40 large textbook sized bindings done by the end of the day.
This is roughly 2-3 hours of work, ordered an hour and a half before closing on a Sunday, where we close early. Each book needs to be printed, then given a front and back cover, then hole punched about 10-25 pages at a time in the comb binder. If too many pages are in the machine it could ruin the pages and new copies would need to be made, or worse the machine could jam. The solution was to use our staff wisely. I was binding and making copies of the book, while my co worker would punch the holes for the comb binds, a third associate was taking care of every customer themselves. They were acting as a defense to make sure that the massive order is done by the deadline. We finished the order on time and got the customer what they needed. - An order comes in every once in a while with this same issue, a card is ordered with no bleed.
Generally customers do not understand how important bleed edges are for printing so edits need to be made to reorient content to be within bleed lines. It happens once in a while on cards but it is mostly business cards. We always call the customer to let them know what we are doing and always make sure all the content is all set and present. Nothing can be cut off and the customer always gets usable cards for what they’re ordering.